Our expertise spans the entire supply chain process, from sourcing, purchasing, transportation and logistics, to inventory control, inspection and quality assurance. Every product and service we use must comply with our strict quality and safety requirements. In addition to our procurement offices, we operate and maintain fabrication facilities for manufacturing bespoke components and lay-down yards for storing material and equipment.
We have strategic manufacturing partners who provide the latest products to the market at partner discounted rates. We also employ a well-developed corporate social responsibility program to actively seek to engage local suppliers wherever possible and are committed to providing global opportunities for our supply chain. We are advocates of local distribution of wealth and investment locally.
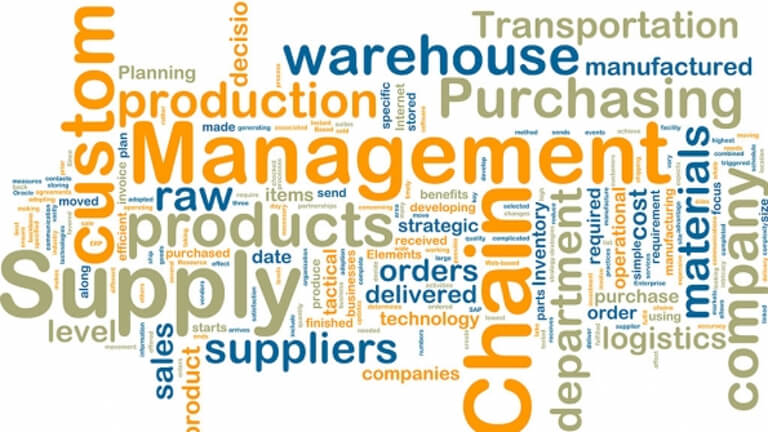
We utilize competitive bidding and negotiate long-term agreements to obtain competitive prices for equipment, material and services. We also do our homework, extensively researching markets and suppliers to ensure we prepare accurate estimates, select the best products at commercially viable rates.
Having an in-house Order Management System (OMS) streamlines the entire supply chain process for ordering equipment & material and ensures every aspect of the process is documented with up to date information for our customers. We work in industries where operational demands dictate lead times and having an effective operational environment is key to meeting the expectations of our clients.
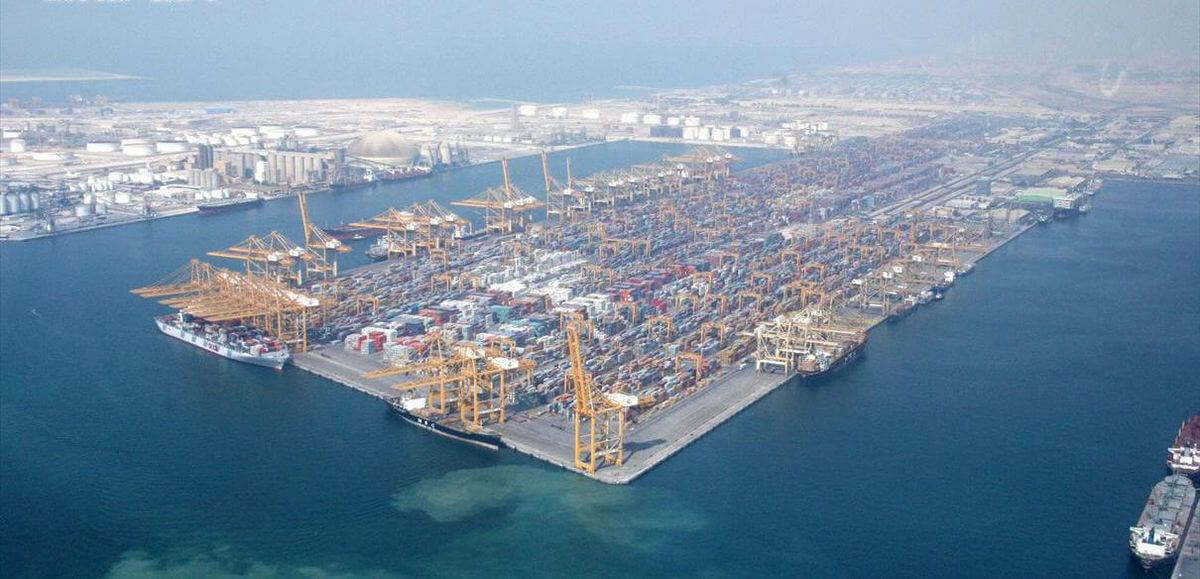
These are some features for just two components of the OMS.
Procurement
- Time‐phased DRP
- Centralized purchasing
- Online requisitions
- Blanket purchase orders
- Drop shipments
- Purchase price variance
- Landed costing
- Freight accruals
- Vendor performance tracking
Warehouse & Transportation Management
- Multiple warehouse & inventory control
- Stock availability
- Directed activities for labour optimization
- Physical inventory and cycle counting
- User defined unit of measures
- Dimensional inventory
- Quality inspection with pass/fail hold
- Order tracking
- Expiration dates
- Serialization
- MSDS tracking and reporting
- License plating ‐ single level or nested
- RMAs
- Vendor managed inventories (VMI)